3D Reverse Engineering Services
Reverse engineering can be used to recreate or reproduce a physical object by capturing its dimensions and geometry through 3D scanning techniques. It is utilized to replicate the object, enhance and optimize existing designs, or systems to uncover its underlying principles and mechanisms. With 3D digital data at our disposal, the range of applications becomes essentially limitless once the limitations imposed by conventional measurement technologies are eliminated.
The technique of 3D Scanning involves using equipment that measures the distance between the scanner and the object using a laser or other light source to digitally record information about the shape of the thing. Very small things all the way up to full-size Aeroplan's can be captured with 3D scanning. We can quickly inspect parts thanks to 3D Laser Scanners, which can gather tens of thousands of points per second.
At RA Global, we have been providing industry-leading 3D Scanning and Reverse Engineering Services in Mumbai to a variety of industries since 2013. Our expertise in capturing data for Marine, Industrial, Manufacturing, and Automotive applications ensures you have an expert reverse engineer you can rely on.
Contact Us today for your 3D Scanning and Reverse Engineering requirements.
What is Reverse Engineering?
Reverse engineering refers to the process of creating a digital 3D design CAD model of an existing physical object that accurately represents the geometry and details of the original object.
This CAD model can then be used to reproduce the object, modify and improve and optimize existing designs, or create new products based on the form and functionality of existing ones.
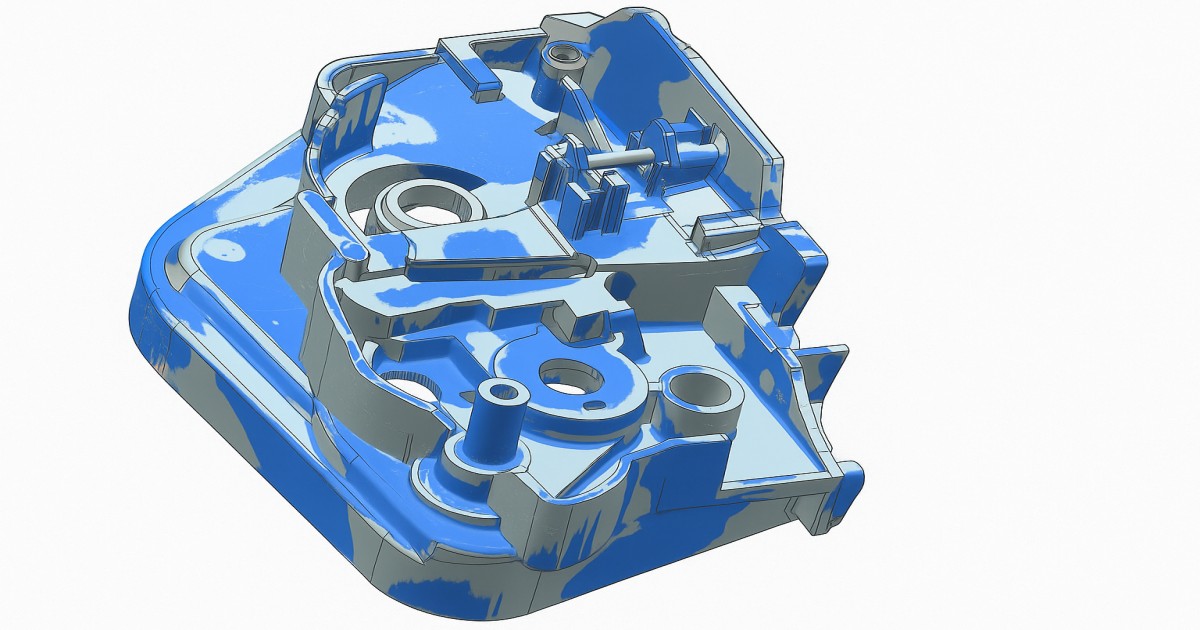
Reverse Engineering Methodologies
-
Product Analysis: RA Global employs skilled reverse engineers who can analyze and evaluate the design, components, and functionality of a product or system. Through their expertise, they can dissect and understand how the product works, allowing clients to gain valuable insights into its inner workings.
-
Documentation: Reverse engineering often involves creating detailed documentation and specifications of the analyzed product. At RA Global, we can assist in generating accurate as-built documentation, including CAD models, technical drawings, and assembly instructions. This documentation is essential for replication, modification, or further development.
-
3D Scanning: RA Global utilizes advanced 3D scanning technologies to capture the physical dimensions and geometry of objects. This enables them to create precise digital models, which can be used for analysis, modification, or replication. Metrology techniques ensure accuracy and reliability in the measurements taken.
-
Reconstruction: Convert the processed scan data into a 3D model. This involves creating a surface model by connecting the points or vertices from the point cloud or mesh data. Various software tools, such as CAD software, are used to reconstruct the object digitally. If required, add parametric features to the 3D model, allowing for flexibility in design modifications or adaptations.
-
Competitive Analysis: RA Global helps businesses gain a competitive edge by conducting reverse engineering on competitors' products. By studying their features, design, and manufacturing processes, clients can gain valuable insights for product improvement, innovation, or market differentiation.
-
Rapid Prototyping: Rapid prototyping process is often utilized in reverse engineering to efficiently recreate physical objects or systems based on the data obtained from the analysis.
Solutions to Quick and Accurate Reverse Engineering
What should you do if you need to make or construct a replacement for an existing part, tool, or object but lack the CAD file or design blueprint for it? What if the plans that are currently on file are poor and don't match the final product? Reverse engineering is the solution in both the situations.
Reverse engineering is revolutionized by the use of 3D data capture, which enables users to digitize complex geometries quickly and produce digital models that may be used as design files in the future.
Rapid Prototyping in the manufacture of plastics, component part design revisions or retrofits in aerospace assembly, and the creation of mesh or CAD models of car interiors are just a few of the many applications. Once developed, the digital files can help with the manufacture of aftermarket components, 3D Printing, machining, the construction of molds and patterns, tools, and part inspection.
Our team of experts in reverse engineering services generates 3D CAD models from existing objects (as-built), whether to determine the original design intent, modernize manufacturing processes, or design a new part to fit a legacy part, for instance.
We help our customers by utilizing the appropriate reverse engineering tools, to deliver 3D CAD models and STL files at any point of the Product Development process.
-
3D modeling of objects of all sizes
-
Using generic or native file formats for parametric 3D modeling
-
3-D reconstruction scanning information, sketches, 2D drawings, etc.
-
Hybrid modeling (design intent and as-built)
-
Design modification from existing objects
-
Data preparation for simulation
-
Class-A surface modeling and Class-B surfacing
-
Part design for injection molding (e.g. draft angle analysis, shrinkage)
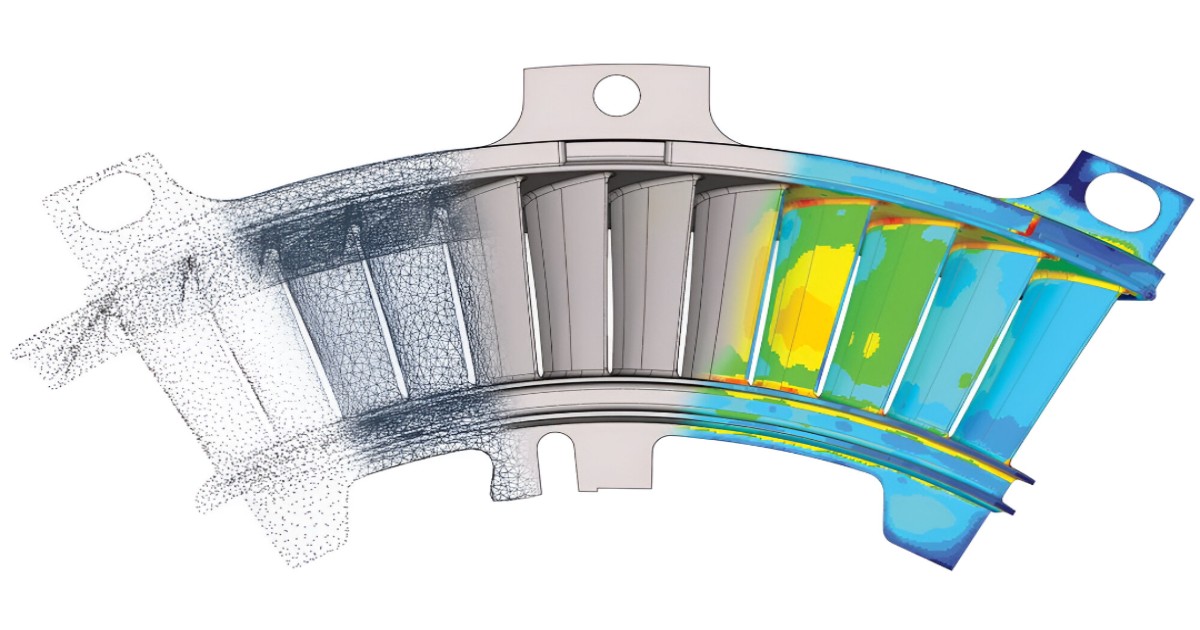
Applications
-
Obsolete and Prototype Parts: 3D reverse engineering is used to create digital models of outdated or complex parts for reproduction or redesign. This includes, Creating digital models of legacy parts that are no longer in production, enabling businesses to reproduce or redesign them, Creating digital models of complex parts with intricate geometries, enabling businesses to analyze and optimize their design, Creating digital models of prototype parts, enabling businesses to test and validate their design before production.
-
Manufacturing and Industrial: 3D reverse engineering is used to streamline production and quality control processes through precise digital modeling. This includes, Creating digital models of products to inspect and analyze their quality, enabling businesses to identify defects and improve product quality, Creating digital models of production lines, enabling businesses to optimize their production processes and reduce costs, Creating digital models of existing products, enabling businesses to analyze and improve their design.
-
Art and Reproductions: 3D reverse engineering is used to preserve and reproduce cultural heritage artifacts, artworks, and historical objects. This includes, Creating digital models of cultural heritage artifacts, enabling businesses to preserve them for future generations, Creating physical reproductions of cultural heritage artifacts, enabling businesses to share them with a wider audience, Creating digital models of damaged or deteriorated artifacts, enabling businesses to restore them to their original state.
-
Medical and Dental: 3D reverse engineering is used to create customized implants, prosthetics, and orthodontic models. This includes, Creating digital models of implants, enabling businesses to design and manufacture customized implants that fit individual patients' needs, Creating digital models of prosthetics, enabling businesses to design and manufacture customized prosthetics that fit individual patients' needs, Creating digital models of orthodontic appliances, enabling businesses to design and manufacture customized orthodontic models that fit individual patients' needs.
In engineering and manufacturing industries, reverse engineering typically produces output in the form of a mesh (STL file), NURBS surface, or a 3D CAD model. The CAD model can be either static or parametric and is commonly saved in STEP, IGES, or Parasolid file formats.
Reverse engineering, product development, and computer-aided simulation can all benefit from 3D scanning (CAE). It is helpful for reverse engineering, Product Designing, measuring complex curved surfaces, quality monitoring, prototyping, and development of industrial tools and devices.
3D Reverse Engineering Services in Mumbai, India
Contact Us for 3D Scanning and Reverse Engineering requirements, ensure to send us the photos and overall dimensions, and desired file type required.
Frequently Asked Questions
What is reverse engineering?
It involves analyzing existing parts or products to create accurate CAD models, enabling reproduction, redesign, or improvement of complex components.
Why choose RA Global for reverse engineering?
We combine advanced 3D scanning, expert CAD modeling, and industry experience to deliver precise, ready‑to‑manufacture digital models efficiently.
Which industries need reverse engineering?
Automotive, aerospace, industrial equipment, manufacturing, and heritage restoration often use it to recreate, update, or improve parts and assemblies.
Can you work from physical samples only?
Yes! We can scan and measure physical components directly, even without original drawings, to build detailed and editable 3D CAD models.
What deliverables do you provide?
We supply 3D CAD models, 2D drawings, and detailed documentation in formats compatible with your design, manufacturing, and quality processes.