Investment Casting
Investment casting, a precision technique also known as lost-wax casting, boasts a rich history spanning decades. This manufacturing process involves creating a wax pattern that shapes a disposable ceramic mould, ideal for producing intricate metal parts in various shapes at scale. The wax model accurately represents the final product, offering several advantages. It yields parts with superior surface finish, tight tolerances, and complex designs, making it indispensable across industries like marine engineering, aerospace, and automobile assembly. Its capability to produce detailed parts with minimal secondary operations underscores its value in modern manufacturing.
What is Investment Casting?
Investment casting is a manufacturing technique where a wax pattern is covered with a refractory ceramic material. Once the ceramic material has dried and hardened, the wax is melted and removed, leaving behind a cavity that matches the final product's geometry. Molten metal is then poured into this cavity, which cools and solidifies to form the metal casting. The ceramic shell is subsequently removed from the metal, resulting in a near-net precision metal component. This method is widely used across various industries due to its ability to produce complex parts with precise dimensions and a smooth surface finish.
Process
Investment casting is a complex production method that produces finely detailed metal parts. In this process, there are 9 steps involved
Wax Making: A wax pattern is made, which is then used to inject the wax material into the aluminium mold, resulting in the exact shape and dimensions of the final product. This wax pattern serves as the base for the whole casting procedure.
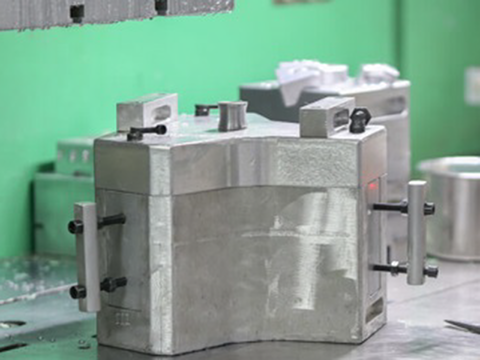
Wax Assembly: These patterns are mounted on a pouring cup and joined by a "gate" to a central wax stick known as a "tree" or "sprue" to form a casting cluster or assembly.
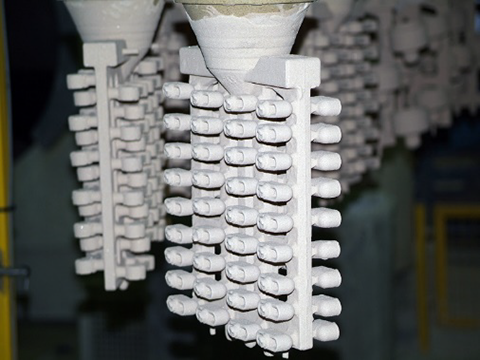
Investment: In this method, the pattern assembly is dipped into ceramic slurry until multiple layers of refractory materials are applied. Note that before applying the next layer, each layer needs to be sufficiently dry. This may result in a thick, robust ceramic shell that protects the delicate wax designs.
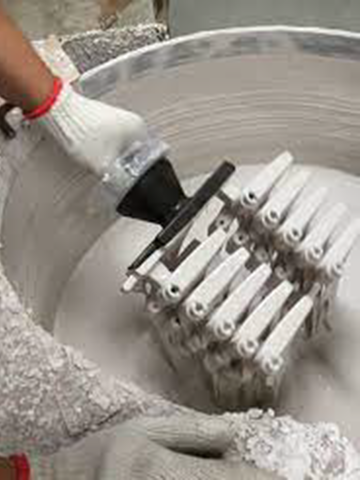
De-waxing: After the ceramic dries, the wax is melted in an autoclave to leave the assembly inside the shell in negative form. After that, the shell mold is burned in an oven at a high temperature
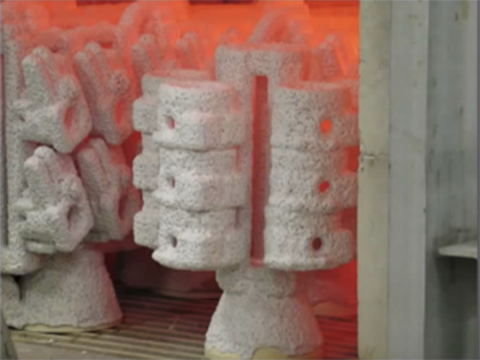
Casting: A molten metal is injected into the shell using a variety of materials and techniques. As the metal cools, the parts, gates, tree, and pouring cup solidify into castings.
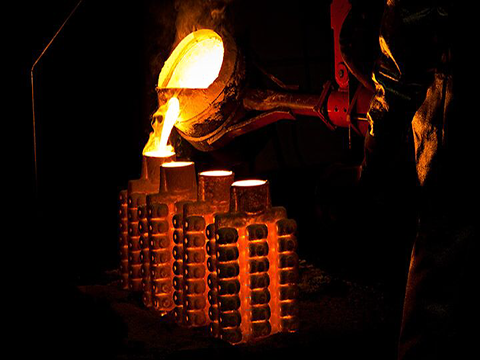
Knock Out: Vibration or water blasting are used to break off the ceramic shell after the metal has cooled and solidified.
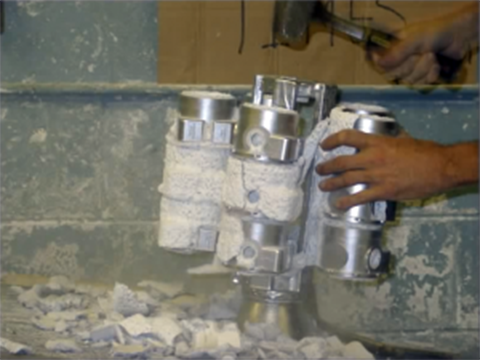
Cut Off : A parts are cut away from the central tree using a high power saw blade.
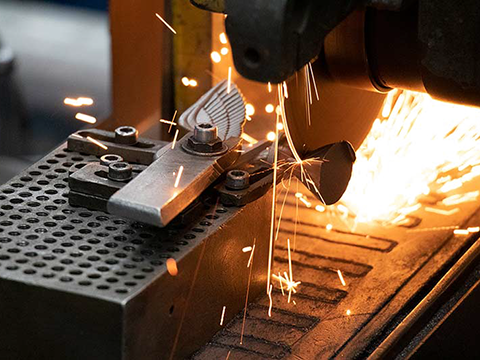
Finishing: In order to create a metal casting that is exactly like the original wax pattern, minor finishing procedures like fettling and grinding are performed.
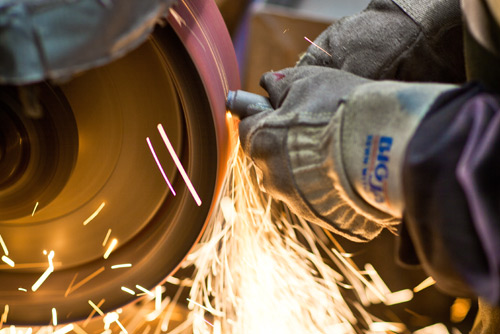
Inspection: The completed part will next be examined with gauges, calipers, a CMM or 3D laser scanning for additional analysis to look for surface flaws and imperfections.
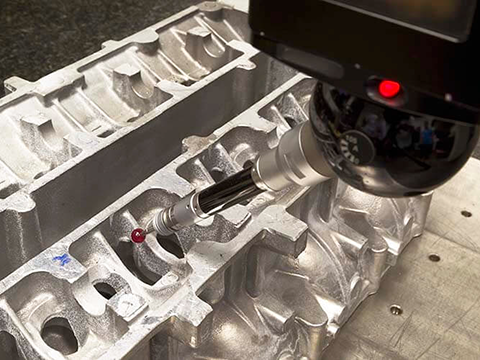
Materials
When it comes to investment casing, there is a wide range of alloys available for selection. These include:
-
Stainless Steel: Comparing stainless steel to many other materials, stainless steel has greater durability. Because of the material's potential, designers and engineers are using investment casting more frequently. Stainless steel finds use in golf club heads, differential gears, gearbox parts for automotive applications, and camp components.
-
Low Alloy Steel: Low alloy steels are widely utilized in mechanical applications due to their cost-effectiveness and advantageous mechanical characteristics. Specialized heat-treating processes allow for the engineering of varying properties in different regions of a single workpiece. This enables the creation of surfaces with specific attributes such as toughness and impact resistance in one area, while enhancing wear resistance in another.
-
Aluminium Alloy: Aluminium alloy is extensively utilized in investment casting, with prominent applications in industries such as aerospace, electronics, and military sectors. The availability of high-quality castings made from aluminium-silicon-magnesium alloy, renowned for its enhanced strength, has facilitated its use in demanding applications like airframe components.
-
Carbon Steel: Carbon steel is a widely used economical material available in various grades distinguished by their carbon content. In industrial applications, heat treatment is employed to enhance its strength, ductility, and overall performance. Its ferromagnetic properties make carbon steel suitable for use in motors and electrical appliances. Known for its structural integrity, safety, and durability, carbon steel remains a preferred choice globally across diverse industries.
-
Cast Iron: Iron castings are renowned for their excellent accuracy and reasonable cost. These castings frequently consist of grey and ductile iron. Although ductile iron is more difficult to produce than other steels, it has superior strength, toughness, and heat resistance. Compared to cast steel, this results in a higher production cost.
RA Global: Your Partner for Investment Casting Services
The Advantage we offer at RA Global offers premium investment cast parts in a range of ferrous and non-ferrous alloys are available . We also perform the necessary secondary operations, such as heat treatment, finish machining, and surface treatment, on the cast pieces
RA Global can work with carbon steel, low-alloy steel, stainless steel grades, and a wide variety of non-ferrous metals, such as aluminium, brass, and bronze. The management team consists of a flexible team of dedicated, technically and commercially sound, experienced, and seasoned managers who enable the delivery of superior goods and services.
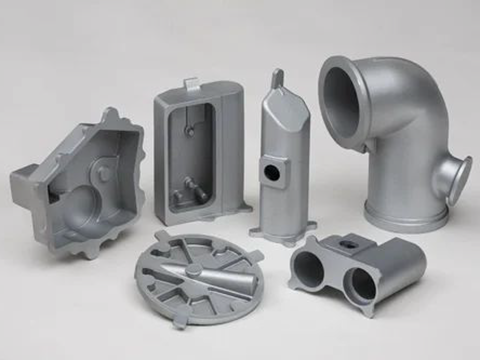
Testing Facility
-
Chemical Analysis
-
Tensile Testing
-
Impact Testing
-
Hardness Testing
Products
-
Food Processing Equipment
-
Gas Turbines
-
Aeronautical Industry
-
Human Implants
-
Industrial Valves
-
Automobile Parts
-
Mining Machinery
-
Different types of components developed for various industries.
Material Handled
-
Magnetic Stainless Steels
-
Hastelloy, Inconel, Monel
-
Nickel /Nickel base alloy
-
Heat Resisting Steels
-
Duplex/Super Duplex Steels
-
Carbon Steels
-
Cobalt Base alloy (Stellite)
-
Nickel Chromium Steels
-
Stainless Steels
-
Copper/Cupro Nickel
-
Non Ferrous Aluminium Phosphorous Bronze
Frequently Asked Questions
What is investment casting?
It’s a precision manufacturing process that creates complex metal parts by pouring molten metal into ceramic molds formed around wax patterns.
Why choose RA Global for investment casting?
We deliver high‑quality cast parts with fine detail, tight tolerances, and smooth finishes, supported by expert engineering and strict quality control.
Which industries use investment casting?
Aerospace, automotive, industrial machinery, medical devices, and energy sectors benefit from durable, complex, and lightweight metal parts made this way.
What materials can you cast?
Stainless steel, carbon steel, aluminum, bronze, and specialized alloys based on your project’s strength, temperature resistance, and design needs.
Can you produce both prototypes and production runs?
Yes! We support small batches for prototyping and scalable production volumes to meet diverse customer requirements efficiently.